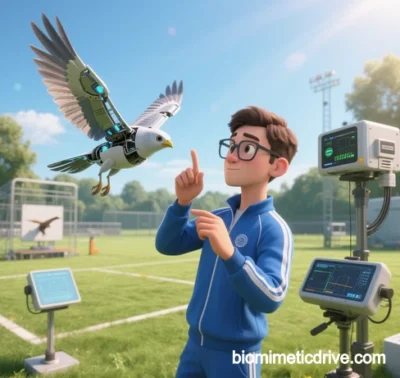
Biomimetic Drive: The Core of Next-Generation Intelligent Machinery
Biomimetic drive systems, which mimic the motion mechanisms, energy conversion modes, and environmental adaptability of living organisms, are redefining the design paradigms of intelligent machinery. Their core value lies not only in structural imitation but also in achieving breakthroughs in efficiency, flexibility, and environmental adaptability through multi-scale bionic integration (molecular-tissue-organ), smart material innovation, and bio-electromechanical coupling. Below is an in-depth analysis of their technical principles, applications, challenges, and industrial trends.
I. Technical Principles: Cross-Scale Bionics from Molecules to Swarm Intelligence
Molecular-Level Innovations
- Piezoelectric Ceramic (PZT) Actuation: Mimicking fish muscle contraction, PZT materials generate micron-level deformation under electric fields to drive robotic tails for efficient deep-sea propulsion.
- Ionic Polymer-Metal Composites (IPMC): Inspired by octopus tentacle movement, IPMC achieves muscle-like contractions at 1–3V with 45% energy conversion efficiency.
Tissue-Level Structural Design
- Hierarchical Actuation: Leveraging insect flight muscle fiber arrangements, gradient-stiffness actuators triple torque output at equivalent power (e.g., bionic exoskeleton knees).
- Energy Metabolism Optimization: Biofuel cells mimicking mitochondrial ATP synthesis double underwater robot endurance compared to traditional systems.
Swarm Intelligence
- Hive-Mind Algorithms: Enable distributed multi-robot collaboration (e.g., construction site logistics), improving fault tolerance by 60% and task completion speed by 45%.
II. Cross-Domain Applications: From Healthcare to Space Exploration
Healthcare
- Bionic Prosthetics & Exoskeletons:
- Carbon fiber-shape memory alloy hands achieve 0.1N grip precision with 27 fine motor modes (e.g., holding pens or keys).
- Brain-computer interface (BCI) drivers reduce exoskeleton gait-switching latency to 80ms, nearing biological neural speeds.
- Surgical Robotics: Pneumatic artificial muscle arrays enable snake-like arms to navigate 5mm spaces for minimally invasive cardiac surgery.
Extreme Environment Exploration
- Deep-Sea Robots:
- Manta ray-inspired soft robots with IPMC-driven pectoral fins dive to 11,000 meters, outperforming hydraulic systems in pressure resistance.
- Ocean thermal energy modules enable 30-day autonomous operation in the Mariana Trench.
- Space Exploration: NASA’s LEMUR robots use bio-inspired climbing feet with molecular-scale adhesion for Martian cliff sampling.
Industrial Manufacturing
- Flexible Assembly Lines: Tendon-bone mimicry enables six-axis robots with ±0.02mm precision for chip packaging.
- Self-Healing Joints: Microcapsule-embedded bionic joints withstand high-temperature wear for 8,000-hour lifespans.
III. Challenges and Breakthrough Pathways
Material-Driver Coupling
- Issue: Trade-offs between efficiency and durability (e.g., IPMC performance drops 50% in >80% humidity).
- Solutions:
- Graphene-hydrogel composites adapt stiffness via hydrogen bond density, improving environmental resilience by 70%.
- 4D printing streamlines stimulus-responsive material fabrication, cutting production cycles by 90%.
Bio-Mechanical Interfaces
- Issue: BCI signal delays (~200ms) hinder real-time control.
- Solutions:
- Spiking Neural Networks (SNN) reduce processing latency to 15ms via pulse-based encoding.
- Memristor-based synaptic chips cut energy use to 1% of traditional processors.
Energy Supply Revolution
- Mitochondrial Batteries: Synthetic biology-driven cells achieve 500Wh/kg density (3x lithium batteries).
- Multi-Modal Harvesting: Integrated piezoelectric-thermoelectric-photovoltaic systems enable desert robots to self-power indefinitely.
IV. Industry Trends and Future Outlook
Market Growth
- The global biomimetic drive market will grow at 18.7% annually, reaching $235B by 2030, led by healthcare (35%), manufacturing (28%), and aerospace (20%).
Technology Convergence
- Neuromorphic Computing + Drives: Intel’s Loihi chips enable sub-millisecond reflexes for autonomous vehicle collision avoidance.
- Quantum Sensing: Diamond NV-center torque sensors achieve 10^-9 N·m precision in bionic joints.
Ethics and Standards
- Bio-Mechanical Ethics: Frameworks needed for neural-integrated prosthetics to address consciousness-related legal debates.
- Interoperability: ISO/TC 299 standardization to unify cross-platform biomimetic interfaces.
V. Decadal Milestones
2026–2028
- All-day exoskeletons (<1.5kg, 72h battery) revolutionize rehabilitation.
- Deep-sea mining robots with muscle-like hydraulics quintuple efficiency.
2029–2032
- Synthetic biology drives ATP-powered nanobots for targeted drug delivery.
- Lunar base construction with swarm robots achieves millimeter-precision regolith 3D printing.
2033–2035
- Consciousness-driven prosthetics with tactile feedback blur human-machine boundaries.
- Quantum-computer-integrated biomimetic systems enable self-evolving fourth-gen AI machinery.
Conclusion: The Symphony of Biology and Machines
Biomimetic drive systems transcend traditional electromechanical limits through a three-phase evolution: structural mimicry → functional超越 → intelligent symbiosis. As joints gain muscle-like flexibility, drivers harness cellular metabolism, and controls mirror neural adaptability, we witness the fusion of life’s principles with engineering. This redefines “intelligence”—future machinery will not be mere tools but energy-information entities embodying billions of years of evolutionary wisdom.
Data sourced from public references. For collaboration or domain inquiries, contact: chuanchuan810@gmail.com