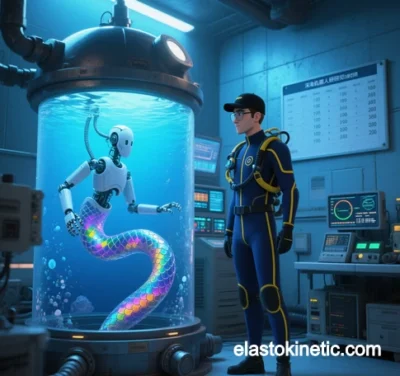
Latest Applications of Elastokinetics in Soft Robotics (2025)
Elastokinetic technology—integrating elastic material properties with actuation mechanisms—is driving breakthroughs in soft robotics, enabling high adaptability, energy efficiency, and intelligence. Below are cutting-edge applications across healthcare, industry, extreme environments, and defense:
I. Healthcare: Minimally Invasive Surgery and Rehabilitation
1. Hyperelastic Torque-Reversal Joints
- Core Technology: Transient bistability in soft joints enables reversible torque switching via nonlinear elastic deformation, achieving low energy consumption (<1 W) and high precision (±0.1 mm positioning).
- Case Study: Imperial College London’s endoscopic surgical robot (2025) uses PDMS-shape memory alloy composite tools for 360° articulation in human cavities, minimizing tissue damage.
2. Elastic-Driven Neurorehabilitation Exoskeletons
- Core Technology: Antagonistic electroactive polymer (EAP) and magnetorheological elastomer (MRE) designs mimic muscle force-velocity relationships, paired with spiking neural networks (SNNs) for real-time motion intent analysis.
- Case Study: Ekso Bionics’ NeuroFlex glove employs dielectric elastomer actuators (DEAs) to assist 0°–120° finger flexion in spinal injury patients, reducing energy use by 60% vs. hydraulic systems.
II. Industry: Adaptive Grasping and Cobots
1. Variable-Stiffness Soft Grippers
- Core Technology: Magnetorheological elastomers switch between soft (1 kPa) and rigid (1 MPa) states in 0.1 seconds via external magnetic fields for delicate object handling.
- Case Study: Festo’s OmniGrip Pro integrates multimodal sensors and elastokinetic models to grip objects from eggs to metal parts, with 10 kg payload and ±0.05 mm precision.
2. Modular Reconfigurable Robotic Arms
- Core Technology: Origami-inspired pneumatic joints with PDMS-nylon composites enable multi-DOF motion through folding/unfolding.
- Case Study: MIT’s ReBot autonomously switches tools (welding, handling, inspection) on assembly lines, cutting energy use by 40%.
III. Extreme Environments: Deep Sea and Space
1. Deep-Sea Exploration Robots
- Core Technology: Ionic polymer-metal composites (IPMCs) and liquid metal elasthers enable motorless propulsion under 1,500-meter water pressure and sub-zero temperatures.
- Case Study: Harbin Engineering University’s DeepOcto, an octopus-inspired robot with eight IPMC tentacles, performs sample collection and mapping at hydrothermal vents for 72 hours.
2. Space-Deployable Structures
- Core Technology: Nitinol-carbon nanotube aerogel composites fold/unfold via photothermal actuation, reducing energy use by 45% in zero gravity.
- Case Study: ESA’s SolarSail satellite deploys 100 m² elastokinetic solar sails weighing 2 kg for deep-space missions.
IV. Defense and Rescue: High-Dynamic Exoskeletons
1. Soldier Augmentation Exoskeletons
- Core Technology: Liquid crystal elastomer (LCE) “artificial tendons” achieve 5 kW/kg power density via light-electric-thermal coupling, nearing 1.5x biological muscle performance.
- Case Study: DARPA’s Atlas Exoskeleton enhances soldier load capacity to 100 kg and mobility to 15 km/h for mountain warfare, with IR-visible dual-mode imaging.
2. Disaster Rescue Robots
- Core Technology: Marangoni effect-driven surface tension gradients enable rapid movement in rubble.
- Case Study: University of Tokyo’s ResQBot navigates debris with PDMS shells and magnetorheological fluid cores, resisting 500 N impacts while detecting life signs.
V. Challenges and Future Directions
1. Current Limitations
- Material Fatigue: Elastic materials degrade by 15% after 100,000 cycles, necessitating dynamic covalent self-healing systems (e.g., thiol-ene click chemistry).
- Control Complexity: Real-time solving of nonlinear elastokinetic models requires edge AI chips (neuromorphic processors).
2. Emerging Innovations
- Biohybrid Systems: ETH Zurich’s living-mechanical actuators combine LCEs with myoblasts for 2.5 N/cm² contraction force.
- Self-Powered Networks: Triboelectric nanogenerators (TENGs) harvest vibration energy for battery-free operation.
Conclusion
Elastokinetics is redefining the capabilities of soft robotics through material-structure-control synergy, enabling precision surgery, space adaptability, and military augmentation. By 2030, the global market for elastokinetic-driven soft robots is projected to exceed $22 billion, spawning innovations like adaptive-stiffness robots and biohybrid exoskeletons.
Data sourced from public references. For collaboration or domain inquiries, contact: chuanchuan810@gmail.com.