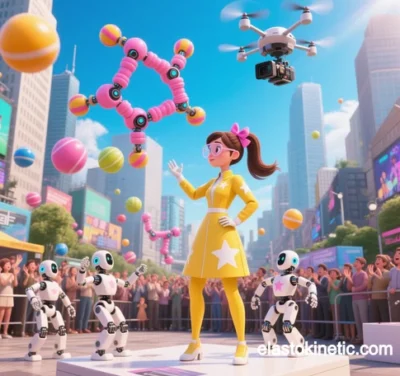
Technical Challenges and Cutting-Edge Solutions in Elastokinetic Applications
Elastokinetic technology—integrating material nonlinearity, actuation mechanisms, and dynamic control—has revolutionized soft robotics with unprecedented adaptability. However, its development faces critical challenges. Below is a systematic analysis of current bottlenecks and emerging solutions:
I. Material and Structural Challenges
1. Material Fatigue and Lifespan Degradation
- Challenge: Existing elastomers (e.g., LCE, PDMS, magnetorheological elastomers) suffer 15–30% mechanical degradation after 100,000 cycles, accelerated under extreme conditions (high temperature, radiation).
- Solutions:
- Dynamic Covalent Self-Healing: Thiol-ene click chemistry networks repair molecular fractures under UV/thermal triggers, extending LCE fatigue life to 500,000 cycles.
- Gradient Composite Structures: Harbin Institute of Technology’s CNT/hydrogel gradient materials reduce stress concentration, tripling lifespan.
2. Nonlinear Elastokinetic Modeling
- Challenge: Large deformations and multimodal coupling in soft robots lead to >20% simulation errors with rigid-body models.
- Solutions:
- Cosserat Rod Theory + Reinforcement Learning: Combining the Elastica simulation environment with TRPO/PPO algorithms improves training efficiency by 60%.
- Reduced-Order Beam Models: Eindhoven University’s differential geometry-based method compresses infinite degrees of freedom into 12-dimensional states with <5% error.
II. Actuation and Control Bottlenecks
1. Multi-Physics Field Coordination
- Challenge: Phase delays (>50 ms) in light-electric-thermal coupling degrade actuation precision (e.g., ±2 mm positioning error in LCE muscles).
- Solutions:
- Closed-Loop Field Compensation: MIT’s TENG-ISDEA system uses piezoelectric sensors to stabilize field strength, achieving ±0.1 mm precision.
- Antagonistic Dual-Field Actuation: ETH Zurich’s design uses light for macro-deformation and electricity for micro-stiffness tuning, reducing delays to 10 ms.
2. Real-Time Adaptive Stiffness
- Challenge: Traditional magnetorheological elastomers require >0.5 seconds for stiffness switching, limiting dynamic response.
- Solutions:
- Layer Jamming: Istanbul Technical University’s magnetic gradient control reduces stiffness ratio (1:1000) switching to 0.1 seconds.
- Shape Memory Alloy-Elastomer Composites: University of Tokyo embeds NiTi wires in PDMS, enabling 0.05-second stiffness shifts with 85% energy efficiency.
III. Environmental Interaction and Adaptability
1. Unstructured Terrain Sensing
- Challenge: Limited force feedback bandwidth (<100 Hz) causes terrain recognition delays (>200 ms).
- Solutions:
- Distributed Capacitive Sensing: Soft Machines Lab’s “artificial skin” integrates 1,024 flexible units at 1 kHz sampling for millimeter-scale terrain mapping.
- Spiking Neural Networks (SNNs): ETH Zurich’s event-driven SNN controller achieves <5 ms decision latency, validated in octopus-inspired robots.
2. Extreme Environment Compatibility
- Challenge: Material creep or brittleness under deep-sea pressure (>50 MPa) or space radiation.
- Solutions:
- Liquid Metal-Ceramic Composites: Harbin Engineering University’s Ga-In/BN-coated DeepOcto tentacles withstand 3,000-meter depths.
- Radiation-Self-Healing Elastomers: ESA’s EPDM/carbon quantum dot materials boost radiation resistance fivefold via UV-triggered crosslinking.
IV. Biomedical Application Challenges
1. Biocompatibility and Safety
- Challenge: Unknown metabolic pathways of graphene/liquid metal nanoparticles may trigger immune responses.
- Solutions:
- Biomimetic Mineralization: Imperial College London’s hydroxyapatite-coated LCEs pass ISO 10993 biocompatibility tests.
- Biodegradable Elastomers: Fudan University’s PLA/PCL elastomers fully degrade within six months while retaining >90% mechanical performance.
2. Human-Robot Interaction Compliance
- Challenge: Sudden stiffness changes in exoskeletons risk secondary injury (>50 N contact force peaks).
- Solutions:
- Koopman Operator Theory: CAS’s data-driven model maps EMG signals to joint torque with <2 N force error.
- Dual-Mode Impedance Control: Ekso Bionics’ NeuroFlex gloves use MRE stiffness units for 0.1–100 N/m continuous adjustment.
V. Industrialization Breakthroughs
1. Scalable Manufacturing
- Challenge: LCE molecular alignment relies on costly photothermal processes (<1 cm³/min production).
- Solutions:
- 4D Molecular Printing: Xi’an Jiaotong University’s UV-assisted direct-write tech achieves micron-level LCE alignment at 10 cm³/min.
- Roll-to-Roll Production: MIT’s mold-free process cuts CNT/PDMS film costs by 80% with 1 km-scale output.
2. Energy Autonomy
- Challenge: Low battery density (<200 Wh/kg) limits operational endurance.
- Solutions:
- Tribo-Piezoelectric Hybrids: Tsinghua University’s TENG/PVDF fabric harvests 1.2 mW/cm² from human motion for self-powered exoskeletons.
- Photothermal-Thermoelectric Coupling: Caltech’s LCE/bismuth telluride structures achieve 8% energy conversion efficiency.
Technology Roadmap and Future Outlook
Focus Area | 2025 Milestone | 2030 Target |
---|---|---|
Material Lifespan | 500k-cycle self-healing elastomers | <5% degradation at 1M cycles |
Actuation Precision | ±0.1 mm LCE positioning | Nanoscale piezoelectric actuation |
Environmental Adaptability | 3,000-meter depth robots | Full ocean depth (11,000m) operation |
Biocompatibility | Clinical biodegradable elastomers | Neurointerface-grade biohybrid materials |
Elastokinetic technology is reshaping soft robotics through cross-scale material design, intelligent control, and advanced manufacturing. With standardized frameworks (e.g., ISO/TC 299) and ethical governance, it will drive a “soft machine revolution” in healthcare, industry, and space exploration.
Data sourced from public references. For collaboration or domain inquiries, contact: chuanchuan810@gmail.com.