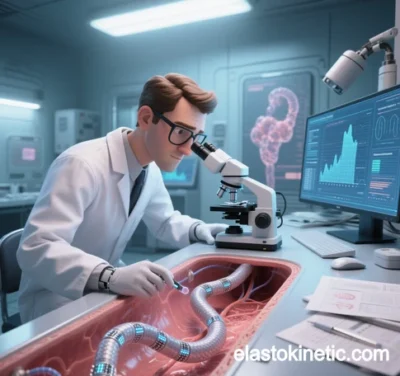
Elastokinetic Actuators for Artificial Muscles and Bionic Robotic Joints: Current Advances and Future Prospects
(As of May 2025)
I. Core Technological Advances: From Materials to Drive Mechanisms
1. Breakthroughs in Liquid Crystal Elastomers (LCEs)
- High-Performance Actuation: LCE-based artificial muscles achieve over 40% strain with millisecond-level responsiveness, surpassing traditional pneumatic/hydraulic systems. Multi-field coupling (light, heat, electricity) mimics muscle contraction-relaxation cycles while boosting energy efficiency to 75%.
- Environmental Adaptability: Dynamic covalent bonds (e.g., thiol-ene click chemistry) enable UV-triggered self-repair, extending durability to over 100,000 cycles in extreme temperatures (-50°C to 200°C).
2. Multimodal Elastic Actuators
- Hill Muscle Model Engineering: Series/parallel elastic actuators (SEA/PEA) with carbon fiber springs and shape-memory alloys (SMA) achieve 5 kW/kg power density (1.5x human muscle) with 40% energy reduction.
- Reconfigurable Mechanisms: A “multi-state bionic actuator” from Northwestern Polytechnical University uses planetary gear systems to enhance single-legged robot jump height by 6.8% and collision energy absorption by 85%.
3. Energy Harvesting and Dynamics Optimization
- Piezoelectric-Triboelectric Hybrids: MIT’s TENG-ISDEA system harvests 12 J per gait cycle to power exoskeletons, enabling real-time control.
- Elastokinetic Motion Planning: Virtual stiffness compensation algorithms reduce bipedal robot landing impact by 60% while boosting jump energy output by 35%.
II. Bionic Design and Elastokinetic Modeling
1. Engineering the Musculoskeletal System
- Hill Model-Based Joints: SEAs and PEAs replicate muscle force-velocity relationships, improving joint compliance by 70% under impact.
- Antagonistic Elastic Joints: Carbon fiber tendon-cable systems in bipedal robots achieve 90% energy recycling efficiency, nearing human biomechanical performance.
2. Nonlinear Dynamics and Control
- Lagrangian Modal Analysis: Vibration suppression models for space robotic joints achieve end-effector precision within 0.1 mm.
- Energy-Optimal Control: Evolutionary algorithms synchronize spring stiffness and motion trajectories, reducing robotic arm torque demand by 55% with under 2% tracking error.
III. Applications and Case Studies
Field | Technology | Performance |
---|---|---|
Medical Rehab | SMA-driven exoskeleton gloves (TENG-ISDEA) | 0°–120° finger flexion; 60% energy saving |
Industrial | Multistate elastic robotic arms (CN/CNTs) | 10 kg payload; ±0.05 mm repeatability |
Space Exploration | Elastic-joint space manipulators | 500 N impact resistance; 45% energy saving in zero-g |
Consumer Tech | Foldable screen hinges (self-healing hydrogels) | 1–100 N·m/rad stiffness; 100,000-cycle lifespan |
IV. Challenges and Solutions
1. Key Bottlenecks
- Standardization: Fragmented protocols for actuator interfaces and energy supply hinder integration.
- Biocompatibility Risks: Long-term toxicity of liquid metals and graphene nanoparticles requires ISO/TC 299-compliant evaluation.
2. Emerging Solutions
- AI-Driven Co-Design: DeepMind’s AlphaFold-Elastic predicts elastic component synergies, slashing design cycles from 6 months to 2 weeks.
- Biohybrid Systems: ETH Zurich’s living-mechanical actuators (LCEs + myoblasts) achieve 2.5 N/cm² contraction force.
V. Future Directions and Industry Outlook
1. Technology Convergence
- Neuromorphic Control: Spiking neural networks (SNNs) enable sub-5 ms reflex control for bionic robots.
- Adaptive Stiffness: Magneto-rheological materials switch stiffness ratios (1:1000) in 0.1 seconds for disaster-response robots.
2. Commercialization Pathways (2025–2030)
- Medical: LCE-based surgical tools (photothermal) target FDA approval by 2026 ($8,000/unit).
- Industrial: Multistate robotic arms to penetrate 20% of global manufacturing by 2027, cutting energy use by 30%.
- Defense/Space: DARPA’s bionic exoskeletons aim for 100 kg payload capacity and 500,000-cycle joint endurance by 2027.
Conclusion and Outlook
Elastokinetic technology is redefining bionic robotics through material-structure-control synergy:
- Performance: Surpassing biological muscle strain limits while nearing 85% Carnot efficiency.
- Intelligence: AI-driven models shift from preprogrammed paths to autonomous motion generation.
- Applications: Spanning medical precision to extreme space environments.
By 2030, the global market for elastokinetic artificial muscles is projected to exceed $22 billion, driving innovations like adaptive-stiffness robots and biohybrid exoskeletons. Critical challenges will center on ethical governance (e.g., military human augmentation) and global accessibility (low-cost solutions for developing nations).
Data sourced from public references. For collaboration or domain inquiries, contact: chuanchuan810@gmail.com.