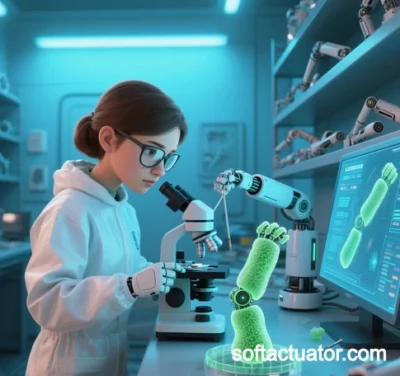
Latest Advances in Bio-Inspired Soft Actuators Mimicking Muscle and Soft Tissue Movement
(Based on 2023–2025 Technological Progress)
I. Bio-Inspired Structural Designs
1. Harvard Wyss Institute: Vacuum-Actuated Muscle-like Actuators (VAMPs)
- Core Technology: Uses vacuum-driven honeycomb-like elastomer structures to mimic skeletal muscle contraction, enabling linear, torsional, or hybrid motion via adjustable air chamber pressure.
- Breakthroughs:
- Matches human skeletal muscle response speed (<100 milliseconds) with >60% efficiency, surpassing traditional pneumatic actuators.
- Self-healing capabilities restore functionality even with 2 mm perforations.
- Applications: Service robots (e.g., elderly assistive grasping) and industrial cobots (safe human-robot collaboration).
2. Northwestern University: Hybrid Soft Actuators (HSAs)
- Design: Combines thermoplastic polyurethane and expandable bellows to replicate muscle “contraction-hardening,” achieving muscle-like power density (500 g load lifted 5,000 times without degradation).
- Innovation:
- Desktop 3D-printed at $3 per unit.
- Worm-like robots (26 cm) navigate narrow pipes at 32 cm/min for disaster rescue.
3. Jilin University: Muscle-Tendon Fluidic Drive System
- Biomechanical Replication: Mimics skeletal muscle force-velocity relationships, delivering 0.32 MPa stress, 40 kg load capacity, and 11.7% strain.
- Validation: Powers exoskeletons with high power density for joint rotation and oscillation.
II. Material and Actuation Innovations
1. Liquid Crystal Elastomers (LCEs)
- Light/Thermal Responsiveness: Programmable 3D motion (e.g., helical artificial fibers mimicking phototropism).
- Self-Sensing: Conductive nanoparticle-LCE composites enable real-time deformation feedback for surgical tools.
2. Nanocellulose-Based Actuators
- Environmental Sensitivity: Humidity/temperature-driven biomimetic crawlers (0.5 cm/s) and self-folding drug delivery devices.
- Biocompatibility: Chitosan coatings enable non-invasive tissue adhesion for wearable rehab devices.
3. Metal-Elastomer Composites
- Muscle-Spring Mimicry: Shape-memory alloys (SMAs) or low-melting-point alloys achieve 200 W/kg power density (near human muscle’s 250 W/kg).
- Case Study: Self-pumping tendon actuators for minimally invasive surgery with 180° bending.
III. Cutting-Edge Applications
Field | Case Study | Advantages |
---|---|---|
Medical Rehab | SanaHeal’s bio-adhesive spring actuators reduce muscle atrophy | In situ mechanical stimulation + non-invasive adhesion |
Soft Robotics | Octopus tentacle robots (Harvard VAMPs) for precision grasping (0.1–5 N adjustable grip) | Safe interaction + multimodal motion |
Environmental Exploration | Helical actuators (HAFMS-TSAs) mimicking plant roots for underground detection | Terrain adaptability + self-feedback |
Aerospace | Distributed soft actuators (U. Washington) for deployable satellite antennas | Energy-efficient + vibration-resistant |
IV. Challenges and Future Directions
1. Key Challenges
- Energy Efficiency: Current actuators under 70% efficiency; bio-inspired ATP-like energy systems needed.
- Miniaturization: Multi-material 3D printing limited to ±50 μm precision.
- Standardization: Lack of unified performance metrics hinders industrial scaling.
2. Emerging Solutions
- Neuro-Muscle Synergy:
- Ionogel circuits for millisecond neural signaling (MIT prototype achieved).
- Reinforcement learning for adaptive soft gripper control.
- Multi-Scale Fabrication:
- Femtosecond laser micro-nano processing for submicron actuators (Max Planck trials).
- 4D-printed thermoresponsive hydrogels for environment-adaptive shapes.
V. Commercialization (2025 Update)
1. Healthcare:
- SanaHeal: Bio-adhesive actuator rehab devices in FDA Phase II trials for post-stroke recovery.
2. Industrial: - Festo: DMSP pneumatic muscle actuators (50 kg load) deployed in automotive assembly.
3. Consumer Tech: - Samsung: LCE-driven self-rolling screens (0.3 mm thick, 2026 launch).
Conclusion
Bio-inspired soft actuators are transitioning from labs to industries, driven by biocompatibility, environmental adaptability, and human-robot safety. Over the next five years, breakthroughs in materials, actuation, and control will revolutionize medical robotics, adaptive exploration, and smart wearables.
Data sourced from public references. For collaboration or domain inquiries, contact: chuanchuan810@gmail.com.