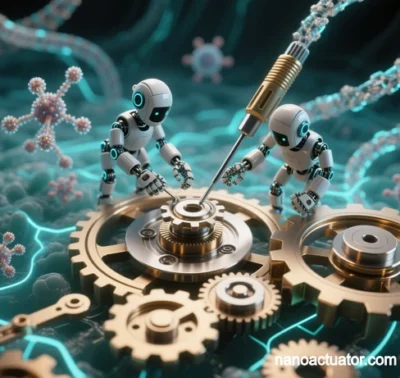
Nanoactuators: Breakthroughs and Applications
Nanoactuators, core components of micro/nano-electromechanical systems (MEMS/NEMS), are redefining the boundaries of mechanical actuation. By converting electrical, magnetic, or chemical energy into precise nanoscale motion, they are revolutionizing fields such as healthcare, robotics, and micro/nano-manufacturing. Below is an analysis of their cutting-edge advancements across applications and technological innovations.
I. Key Applications
- Healthcare and Biotechnology
- Neural Probes and Brain-Machine Interfaces:
Organic semiconductor nanotube (OSNT)-based actuators developed by the University of Houston enhance neural signal recording through electrochemical displacement control, offering potential in epilepsy prediction and neural repair. - Targeted Drug Delivery:
Gold nanoparticle (AuNP) actuators from Finnish researchers use electric fields to modulate DNA conformation, enabling precise drug release with real-time monitoring via surface-enhanced Raman spectroscopy (SERS).
- Neural Probes and Brain-Machine Interfaces:
- Micro/Nano Manufacturing and Optics
- Nanoscale Optical Switches:
MIT’s Ni-Mn-Ga shape-memory alloy actuators achieve ±2 nm waveguide displacement via electrothermal control, advancing tunable photonic chips. - Atomic Force Microscopy (AFM) Calibration:
Electrostatic comb-drive MEMS actuators from Shanghai University provide nanonewton-scale force resolution, standardizing micro/nano-mechanical measurements.
- Nanoscale Optical Switches:
- Robotics
- Soft Robotic Artificial Muscles:
OSNT-based electrochemical actuators achieve 50% strain in liquid electrolytes with sub-100 ms response times, powering octopus-inspired tentacles and microsurgical robots. - Molecular-Scale Manipulation:
The EU’s Mol-Switch project uses ATP-driven DNA-magnetic nanoparticle actuators for single-molecule operations in microfluidics, aiding DNA sequencing and nanodevice assembly.
- Soft Robotic Artificial Muscles:
- Energy and Environment
- Nanopumps and Microfluidics:
NASA’s parallel-plate capacitive actuators enable picoliter-per-minute fluid control for lab-on-a-chip systems. - Energy Harvesting:
Biomimetic prosthetics like the Ottobock Symbionic Leg convert motion into electricity, inspiring self-powered wearables when integrated with nanoactuators.
- Nanopumps and Microfluidics:
II. Technological Breakthroughs
- Material Innovations
- Organic Semiconductor Nanotubes (OSNT):
High conductivity (>10 S/cm) and biocompatibility, with porous structures tripling ion transport rates in liquid environments. - Magnetic Actuation:
Ni-Fe alloy-based actuators from CIC nanoGUNE achieve sub-nanometer precision via magnetostriction, eliminating thermal losses in traditional systems. - Shape-Memory Alloys:
Ni-Mn-Ga films maintain martensitic phase transitions at 10 nm scales, enabling high-density thermal actuators.
- Organic Semiconductor Nanotubes (OSNT):
- Actuation Mechanisms
- Electrochemical Conversion:
OSNT actuators operate at <1 V with 35% energy efficiency, surpassing piezoelectric and electrostatic methods. - Quantum Effects:
AuNP plasmonic resonance enables 0.1 nm particle-substrate spacing control for real-time molecular conformation tracking. - Biomolecular Motors:
ATPase-driven DNA actuators produce micronewton forces for hybrid bio-mechanical systems.
- Electrochemical Conversion:
- System Integration
- MEMS/NEMS Fabrication:
Variable-gap electrostatic comb-drive actuators achieve millinewton forces on 2×2 mm² chips. - 3D Nanoprinting:
Focused electron beam-induced deposition (FEBID) creates complex 10 nm-resolution structures like helical magnetic actuators. - Closed-Loop Control:
Exoskeletons like HAL-ML integrate sEMG and IMU data for real-time gait assistance with <5 ms latency.
- MEMS/NEMS Fabrication:
III. Challenges and Future Trends
- Core Challenges
- Energy Density: Current actuators lag behind biological muscles (3.2 kW/kg), necessitating integrated energy-storage materials.
- Biocompatibility: Implantable electrode signal decay requires solutions like PEDOT:PSS-chitosan hydrogels.
- Manufacturing Scalability: High costs and slow speeds of 3D nanoprinting demand parallel processing and self-assembly techniques.
- Future Directions
- Multi-Physics Actuation: Combine light, magnetic, and electrochemical stimuli for adaptive smart actuators.
- Bio-Mechanical Hybrids: Integrate optogenetics and self-healing materials for autonomous systems.
- Quantum-Mechanical Integration: NV-center diamond probes could enable atomic-scale manipulation and early disease diagnosis.
IV. Technology Comparison
Type | Mechanism | Precision | Response Time | Applications |
---|---|---|---|---|
Electrochemical (OSNT) | Ion intercalation | 1 nm | 10 ms | Soft robotics, neural probes |
Magnetic (NAMMS) | Magnetostriction | 0.5 nm | 1 ms | Nanorobotics, biosensing |
Electrostatic (MEMS) | Coulomb force | 0.1 nm | 100 μs | AFM calibration, optical switching |
Biomolecular (ATPase) | Molecular motor mechanics | Single-molecule | 1 s | DNA sequencing, microfluidics |
Conclusion
Nanoactuators are transitioning from labs to industry, reshaping micro/nano-manipulation and fostering interdisciplinary innovation. Advances in materials, actuation, and integration could soon enable “nano-bio-quantum” systems, revolutionizing healthcare, manufacturing, and energy.
Data sourced from public references. For collaboration or domain inquiries, contact: chuanchuan810@gmail.com