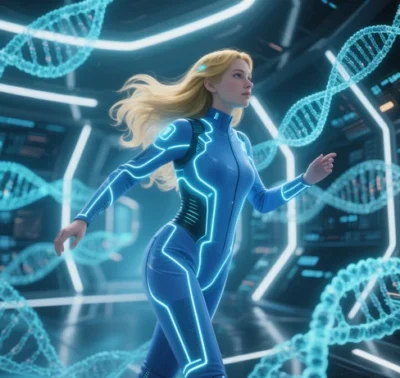
Elastokinetics: Applications and Advances in Biomechanics and Wearable Technology
Elastokinetics, the study of elastic material properties and dynamic mechanical behaviors, is revolutionizing biomechanics and wearable technology by enabling biomimetic tissue simulations and seamless human-device interactions. Below is an analysis of its applications and breakthroughs across these fields.
I. Biomechanical Applications
- Soft Tissue Modeling and Biomimetic Design
- Cardiovascular and Muscular Systems:
Elastokinetics models hyperelastic biodegradable materials (e.g., PLCL elastomers) to simulate dynamic processes like heart contractions and vascular pulsations. For example, elastokinetic-designed degradable cardiac patches conform to myocardial surfaces, monitoring electrical signals and aiding functional recovery. - Neural Interfaces:
4D-printed self-folding neural probes use elastokinetic principles to adaptively wrap nerve bundles via hydration, minimizing implantation damage and enhancing signal precision.
- Cardiovascular and Muscular Systems:
- Dynamic Biomechanical Regulation
- Joint and Bone Stress Distribution:
Elastokinetic models optimize dynamic stress distribution in artificial joints using polyester elastomers (e.g., poly(glycerol sebacate)), reducing wear and extending lifespan. - Cellular Mechanotransduction:
Cyclic stretching of elastic substrates mimics extracellular matrix conditions, guiding stem cell differentiation toward bone or cartilage regeneration.
- Joint and Bone Stress Distribution:
- Biodegradable and Adaptive Implants
- Absorbable Devices:
Transient electronics (e.g., biodegradable pressure sensors) degrade naturally post-use, eliminating removal surgeries. PLCL elastomer scaffolds fully degrade within six months post-fracture healing. - Dynamic Mechanical Adaptation:
Shape-memory polymers (e.g., polycaprolactone) adjust stiffness based on body temperature or pH for disc repair or spinal orthotics.
- Absorbable Devices:
II. Wearable Technology Applications
- Flexible Sensing and Interactive Systems
- Multimodal Sensors:
Elastokinetics enables hybrid material integration (e.g., conductive hydrogels with elastic substrates) for simultaneous strain, pressure, and temperature monitoring. TPU-based ECG patches withstand cyclic strain for long-term cardiac monitoring. - E-Skin:
Biomimetic elastic e-skin with fractal or serpentine circuits achieves ultra-stretchability and self-healing for robotic tactile feedback or prosthetic sensing.
- Multimodal Sensors:
- Energy Harvesting and Dynamic Power
- Mechanical-to-Electrical Conversion:
Dielectric elastomers (e.g., SEBS) optimized via elastokinetics convert motion into electricity, powering wearables with energy densities matching practical needs. - Photo-Thermal Actuation:
Light-responsive elastomers (e.g., azobenzene-modified PDMS) enable self-regulating breathability in smart thermoregulatory fabrics.
- Mechanical-to-Electrical Conversion:
- Biocompatibility and Comfort
- Breathable Substrates:
Ultrathin TPU/PDMS films with microporous designs offer high breathability and skin adhesion. - Interface Optimization:
Gradient modulus designs reduce shear stress at wearer interfaces, preventing skin irritation.
- Breathable Substrates:
- Biomedical-Device Integration
- Drug Delivery and Wound Care:
pH-responsive hydrogel patches dynamically adjust porosity to absorb exudates and release antibiotics on demand. - Neuromuscular Rehabilitation:
Elastic exoskeletons with EMG feedback modulate assistive torque for stroke patients’ gait training.
- Drug Delivery and Wound Care:
III. Technological Breakthroughs
- Material Innovations
- Hyperelastic Biodegradables:
PLCL elastomers achieve controlled degradation and mechanical strength via dynamic covalent bonds. - Smart Responsive Materials:
Liquid crystal elastomers (LCEs) enable light/heat-driven shape-shifting for reconfigurable antennas or adaptive optics.
- Hyperelastic Biodegradables:
- Advanced Manufacturing
- Microfluidic 3D Printing:
Co-deposition of cells and elastic materials creates vascularized tissue scaffolds with micron-scale resolution. - Transfer Printing:
Hybrid elastic circuits (e.g., gold nanowire-elastomer composites) maintain conductivity under extreme stretching.
- Microfluidic 3D Printing:
- Interdisciplinary Synergy
- AI-Driven Design:
Machine learning optimizes elastokinetic parameters (e.g., Young’s modulus) to accelerate material development. - Quantum Computing:
Quantum annealing solves multi-objective elastokinetic equations with unprecedented efficiency.
- AI-Driven Design:
IV. Challenges and Future Directions
- Technical Hurdles
- Fatigue Resistance:
Current elastomers suffer crack propagation under cyclic loading, necessitating self-healing coatings. - Multi-Physics Coupling:
Incomplete models for elastic-electro-thermal-chemical interactions limit reliability in complex environments.
- Fatigue Resistance:
- Clinical and Industrial Barriers
- Long-Term Safety:
Degradation byproducts (e.g., lactic acid) may cause inflammation, requiring kinetic optimization. - Scalable Production:
Roll-to-Roll manufacturing struggles with precision and cost-effectiveness.
- Long-Term Safety:
- Emerging Trends
- Biohybrid Systems:
Integrating engineered cells (e.g., cardiomyocytes) with elastic electronics for self-powered robots. - Metaverse Integration:
Ultra-elastic haptic gloves paired with VR/AR enable immersive virtual interactions.
- Biohybrid Systems:
Conclusion
Elastokinetics bridges materials science, biomechanics, and nanofabrication, redefining medical and wearable technologies. Its breakthroughs in adaptability, biocompatibility, and energy autonomy pave the way for precision medicine, smart wearables, and soft robotics. Future interdisciplinary convergence may birth adaptive life-machine systems, enabling seamless mechanical interactions from cellular to human scales.
Data sourced from public references. For collaboration or domain inquiries, contact: chuanchuan810@gmail.com