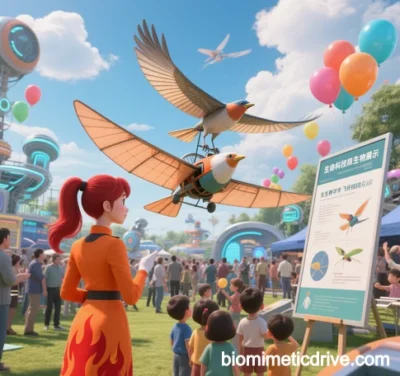
Bio-Mimetic Drive: Cross-Scale Motion Mechanisms and Intelligent Control Paradigms
Bio-mimetic drive technology replicates biological motion patterns, energy conversion mechanisms, and control logic to create multi-scale, high-efficiency motion systems. By merging evolution-optimized energy strategies with engineered designs, it overcomes limitations in flexibility, energy efficiency, and environmental adaptability inherent to traditional mechanical drives. Below is a systematic analysis across four dimensions: motion mechanism emulation, energy conversion paradigms, intelligent control architectures, and cross-domain applications.
1. Cross-Scale Simulation of Biological Motion Mechanisms
Molecular Scale: Cooperative Amplification of Biomolecular Motors
Biological systems convert chemical to mechanical energy through nanoscale protein motors (e.g., ATP synthase, myosin). Researchers at Harbin Institute of Technology developed supramolecular colloidal motors using photo-controlled ATP synthase assemblies. Under light, proton gradients from photophosphorylation drive ATP synthase rotation, inducing self-propulsion (5 μm/s) via asymmetric energy distribution. Light-intensity modulation synchronizes 10⁴–10⁵ molecular motors, amplifying force to micronewton levels, mimicking muscle fiber coordination.
Cellular Scale: Biohybrid Actuators
Tokyo Tech’s muscle-cell-based biohybrid actuators use UV-laser-induced anisotropic myotube alignment to achieve muscle-like contractions (>15% strain). Electric field stimulation regulates calcium channels, enabling cardiac-like rhythmic contractions (0.1–2 Hz) with a power density of 1.2 kW/m³, surpassing pneumatic/hydraulic systems. Combined with 3D-printed scaffolds, these actuators power octopus-inspired robotic arms for multi-DOF grasping (0.3 N grip force).
Tissue Scale: Plant Motion Reverse Engineering
Inspired by plant strategies (e.g., Venus flytrap’s 50 ms closure, pinecone humidity response), bilayer hydrogel heterostructures generate bending moments (curvature >2 mm⁻¹) via light/humidity-driven differential swelling. For example, 4D-printed pinecone mimics autonomously adjust porosity for adaptive thermal management.
2. High-Efficiency Energy Conversion Pathways
Direct Bioenergy-to-Mechanical Conversion
- Molecular Motors: ATP synthase achieves >90% efficiency by rotating γ-subunits via proton flux. Integrated into lipid membranes, these motors drive micron-scale propellers (0.8 pN·s/W efficiency) using light/chemical gradients.
- Muscle Cells: Biohybrid actuators leverage mitochondrial ATP production for actomyosin contraction, tripling traditional motor efficiency.
Indirect Environmental Energy Harvesting
- Light-Driven Micromotors: TiO₂/Janus particles self-propel (20 μm/s) via asymmetric photocatalysis. Au@SiO₂ core-shell motors use NIR photothermal effects for targeted drug delivery.
- Magneto-Thermal Actuation: Xi’an Jiaotong University’s low-voltage (<5 V) artificial muscles combine Fe₃O₄ nanoparticles’ magnetothermal effects with ionogel expansion for dual-mode actuation (12% strain, <1 s response).
3. Neuromuscular-Inspired Control Architectures
Morphological Intelligence
The University of Stuttgart’s “Morphological Intelligence” theory leverages passive stability from biomechanical geometry (e.g., tendon angles, joint curvature). Bio-inspired knee joints with meniscus-like structures autonomously adapt to gait changes, reducing control complexity.
Deep Neural Networks and Biosensor Fusion
UC’s biomechanical-neural model links retinal photoreceptor arrays with muscle signals via deep reinforcement learning (DRL). Virtual models learn complex tasks (e.g., beam walking) with <50 ms latency and 40% lower energy consumption. Zhang Congwu’s cybernetic model integrates feedforward-feedback control, optimizing energy use through breath-muscle synergy.
Adaptive Multimodal Actuators
Biohybrid actuators with optogenetic modules (e.g., ChR2 channels) encode drive intensity via light pulse frequency (0.1–10 Hz). MIT’s ProtoNet meta-learning framework trains actuators to handle perturbations (e.g., sudden flow changes) with <5% stability error using only 50 training samples.
4. Cross-Domain Applications
Medical Robotics
- Targeted Drug Delivery: Magnetic helical nanobots (200 nm diameter) navigate the blood-brain barrier for single-cell precision.
- Rehabilitation Exoskeletons: EMG-driven hybrid exoskeletons adapt to muscle atrophy with <3° gait-matching error.
Environmental Remediation
- Photocatalytic Micromotors: TiO₂ motors degrade pollutants (90% efficiency) while self-propelling for wide-area water treatment.
- Jellyfish Robots: Dielectric elastomer actuators (DEA) enable pulsatile swimming, achieving 5x longer endurance than traditional ROVs.
Advanced Manufacturing
- 4D-Printed Grippers: Humidity-responsive pinecone mimics adjust clamping force (0.1–5 N) for varied surface textures.
- Snake Robots: Segmented artificial muscles enable millimeter-scale crack detection in nuclear pipelines.
5. Challenges and Future Directions
Energy-Lifetime Tradeoffs
Biohybrid actuators face short cell viability (<2 weeks) versus mechanical durability (>10⁶ cycles). Solutions include mitochondrial-mimetic power modules (lipid-encapsulated ATP synthase) and self-healing hydrogels (fracture energy >1,000 J/m²).
Cross-Scale Control Theory
Unifying stochastic molecular motion with macroscopic control requires quantum-classical hybrid simulations (QM/MM-MD) and quantitative metrics for morphological intelligence (e.g., entropy reduction rate).
Ethics and Standardization
Addressing cell source ethics (e.g., iPSCs) and environmental risks of nanobots demands ISO/TC299 standards for biohybrid systems.
Conclusion
Bio-mimetic drive technology is transitioning from structural mimicry to holistic “structure-energy-control” emulation. By integrating synthetic biology (molecular motor engineering), smart materials (4D-printed gels), and neuromorphic computing, three breakthroughs are anticipated within five years:
- Medical-Grade Organs: Fully biocompatible artificial hearts (>5 W power, 10-year lifespan).
- Autonomous Environmental Robots: Solar-powered marine monitoring fish swarms.
- Cross-Scale Manufacturing: Molecular motor-driven nanoscale 3D printing.
This evolution will redefine advanced manufacturing and catalyze “bio-machine” hybrids, blurring the boundaries between life and machinery.
Data sources: Publicly available references. For collaborations or domain inquiries, contact: chuanchuan810@gmail.com.